CASE STUDIES


Case Study 1 - Construction Sector
PVC in window frames
​
​
​
​
​
​
PVC is one of the main polymers used in buildings for its outstanding mechanical and durability properties. However, its production (needing large amounts of chlorine, and forming highly hazardous organochlorinated compounds) and degradation along its lifecycle pose environmental issues that led to global initiatives to reduce PVC consumption.
PU foams are the best isolation material affordable on the present market. It has the potential to replace PVC in some building applications, for example, insulation of window frames, for which IND developed a finished product ready for market. This product is as solid as wooden profiles, so it does not need metal reinforcement as used with PVC (prevents from binding – but is responsible for additional C-footprint). It has proven an extremely high insulating degree, with a Heat Transmittance more than 2 times lower than that of PVC (CE marking test results).
This product is partially bio-based (targets 50-75% overall content of bio-based and renewable materials on a weight basis) using natural oils, lignin and sugars – not competing with ‘higher’ uses according to the biomass value pyramid. In the case of natural oils, those produced for biodiesel industry do not compete with food industry. Lignin is not indeed competing, and sugars are in decline in use in the food industry (sugar industry is looking for new applications out of the food sector). It results in a highly reduced C-footprint of the first life cycle - unlike PVC from fossil sources.
​
​

Case Study 2 - Transportation Sector
Fire resistant epoxy-vitrimer materials for sustainable composites for the railway sector
​
​
​
​
​
​
Fire-resistant epoxy-vitrimer materials for sustainable composites for the railway sector
The interest in using composite materials for structural applications in many different industries has increased significantly in the past decades. Currently, in the railway sector, composites are mainly and extensively used for several interior applications and in secondary structure applications. They would yet have a huge interest as lighter alternatives to metals – enabling less energy consumption.
However, the application of composite materials in rolling stocks (primary structures) is ruled by Fire, Smoke and Toxicity (FST) requirements according to EN45545. As glass- or carbon-based fiber reinforcements have good fire properties, it is mainly the resin that has to be improved regarding fire resistance.
Recently, some composites have been developed that meet these regulations (e.g. Results from Mat4Rail project) but they are not sustainable at end-of-life since they are not intrinsically recyclable. Being thermoset (once cured it cannot be reshuffled), their end-of-life options are very limited, and they normally end up in landfill or incinerated.
​
SURPASS project targets the development of epoxy vitrimers that fulfill all railway FST requirements while meeting the required mechanical performance and being intrinsically recyclable at end-of-life – thus preventing the market from being overflown with emerging non-recyclable composites made up with epoxy-based thermosets.
To overcome this handicap, dynamic covalent chemistries have been applied at the research level during the last decade on thermoset polymers, resulting in innovative unconventional thermoset polymer networks. It is worth noticing that most of the state-of-the-art examples of dynamic thermosets are based on soft, non-structural materials, with a few exceptions: they are not suitable candidates for the railway industry.
​
.png)
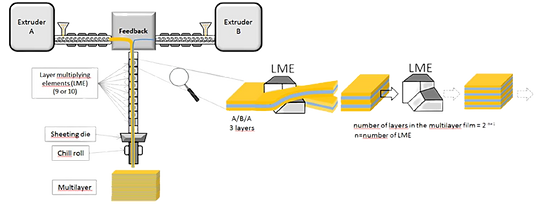

Case Study 3 - Packaging Sector
​
MultiNanoLayered (MNL) films to replace multi-layer films for food packaging
​
​
​
​
​
​
​
Multilayer plastic films are currently used as packaging for the protection of food – because of their unique barrier properties enabling significant extension of food preservation. They are traditionally composed of multiple high-performance layers (e.g. polyolefins (PE (polyethylene) and PP (polypropylene) - 55% of multilayers streams), PA (polyamide), EVOH (Ethylene and Vinyl Alcohol copolymer), etc. but also aluminum or cardboard). Most current designs and the widespread absence of sorting and recycling technologies for such multilayers make them unsuitable for recycling in an economically and environmentally sustainable way.
In addition, chemical compatibility being a key criterion in obtaining quality multilayer films, it is often necessary to use compatibilizer to promote bonds at the interface between the various layers. The MNL process may allow the reduction or remotion of compatibilizers and simplify the nowadays used packaging strategy. SURPASS proposes to evaluate the feasibility of developing MNL-produced polymeric systems. In the MNL process, the combination of polymers at the interfaces is forced by the flows instead of governed by chemical interactions between components (Van der Waals interactions). This effect of nano-structuring allows the realization of multinanocomponent films with good barrier, mechanical and optical properties, theoretically without compatibilizing agents, to reduce material costs and improve the recyclability of the final product.
​
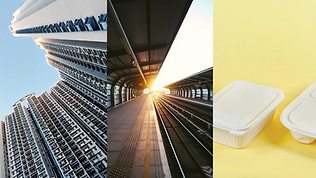